Programmable logic controller:
small box, big effect
A programmable logic controller (PLC) allows you to perform different automation outputs. Sensors are connected to the PLC via input and output modules. The sensors are connected to the inputs on the PLC and transmit the current system status, while the actuators control the system and are connected to the outputs. With the help of a PLC, processes can be monitored and controlled, which is why it forms the central component, or the brain, of automation systems.
Developments are moving towards networked systems that control themselves. Components and machines communicate constantly with one another and with other systems as well, so that the entire value chain is optimised. Even customer and supplier systems are integrated. As a result of networking and data exchange over the Internet of Things (IOT) and the use of automation solutions, the fourth industrial revolution is taking place in the form of Industry 4.0.
Technical versatility for your needs
We expand and develop PLC programmes individually for your machine or system control. Depending on your wishes, we use controllers from PLC manufacturers, Siemens, Schneider-Electric or Rockwell (Allen-Bradley). We are also capable of using the programming of programmable logic controllers based on CodeSys, such as those from Beckhoff or Wago. For the transmission of data, we work with established bus systems such as PROFINET, PROFIBUS, AS-i, Industrial Ethernet, Ethernet/IP, Modbus, Modbus TCP, MQTT and serial interfaces, etc.
We are also flexible with regard to the programming language. Whether LAD (Ladder Diagram), FBD (Function Block Diagram), IL (Instruction List), SCL (Structured Control Language) or ST (Structured Text), we select the right standard for every purpose and adapt to your specifications. This allows new programmes or extensions to be easily integrated into the automation structure already in place at your company.
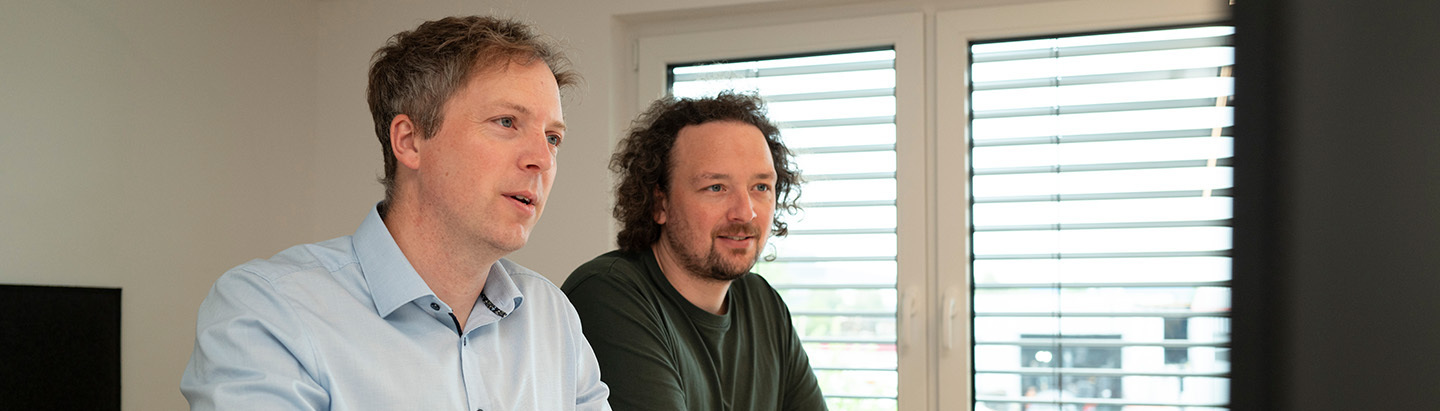
Structured approach to professional solutions
We provide you with support in modernising your production, optimise your systems, take care of the interface connection and provide solutions for challenges that arise. In order to do so, we consider the overall scope of the software project and the functions of the machine before commencing the project. We then work out a suitable software structure based on this. Perfectly thought out, this facilitates the later addition of new functions to the system to expand it and makes sure that the exact time schedule is guaranteed.
When creating software components, we fall back on standard functions that have been well-engineered in long-term tests and use in existing equipment and therefore guarantee a high quality of software. The advantages for you are plain to see: time savings and therefore cost savings for programming, use of proven and optimised functions, and uniform structures in case of several projects.
Based on the risk assessment according to EN ISO 12100, the requisite performance level is determined in accordance with EN ISO 13849-1. We implement these specifications using the corresponding background knowledge. It does not matter how large your system is. We programme small and inexpensive programmes with the same care we do redundant and highly complex large systems or control systems with external data and communication interfaces to control, ERP and visualisation systems.
Our programming skills are used in a variety of projects. In the logistics segment, pallet and container conveyor systems (small parts conveyor technology) as well as stacker cranes and small parts stacker cranes belong to our strengths. Packaging machines, bagging units, (automated) crane systems and handling machines are just a few examples in the mechanical engineering segment where we have developed PLC programmes. Our software is also used for the power supply in the areas of e.g. telecontrol and energy monitoring. Another of our hobby horses is PLC programming for hydraulic steel construction. Our software is used here, amongst other things, for shipping locks, folding bridges and pumping stations.
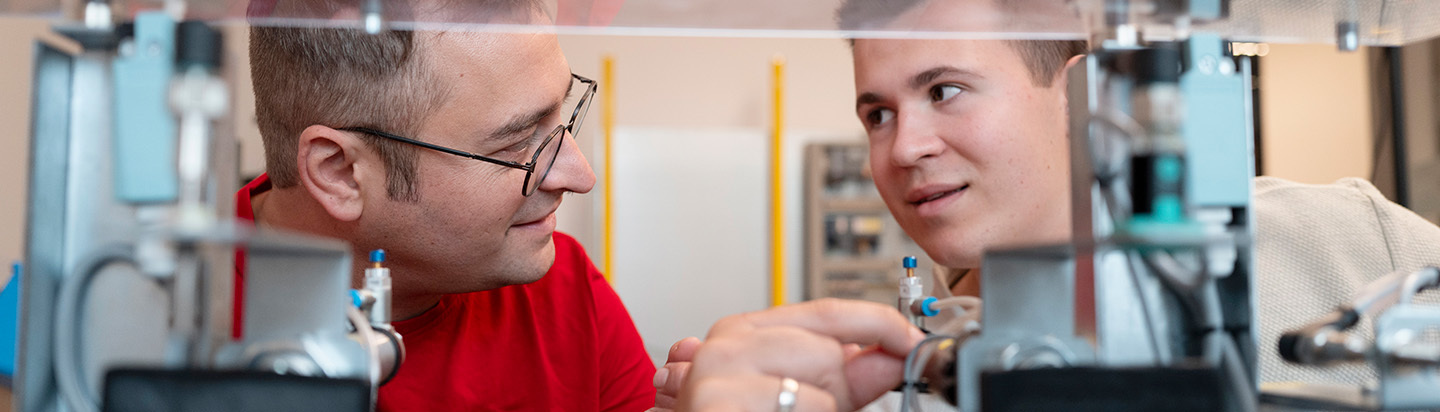
On-site commissioning
Depending on the specifications of the customer, we perform the software implementation and commissioning at the site or directly at the project or system location with the least possible downtime. The numerous start-ups we have performed in various industries means that we can familiarise ourselves quickly with applications, which, amongst other things, pays off when modernising existing systems for our customers.
As you can see, you benefit as a customer throughout the project from the combined expertise of our programming team comprised of young and experienced employees. This transfer of knowledge is one of the reasons for our success. It means that younger colleagues are not left to their own devices, but get to combine their ideas with the expertise of experienced colleagues to create high-quality solutions, no matter who programmes the software.
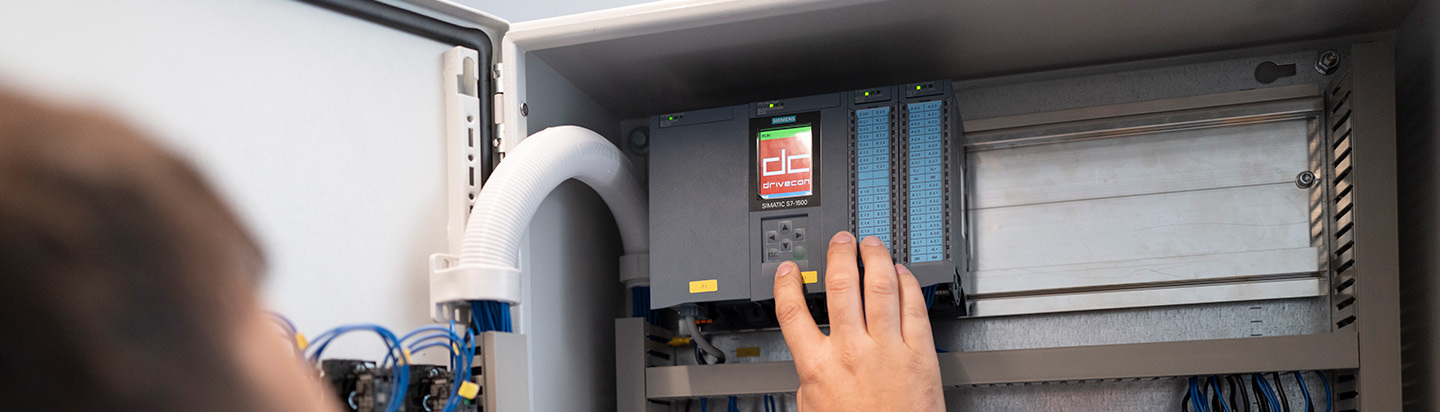
Our services at a glance
- Software extensions to existing facilities and retrofitting
- Software design and programming
- Compliance with standards, regulations, guidelines and international standards
- Fail-safe PLC
- Interface connection
- Uniform software design
- Modular programming
- Use of sophisticated software functions
- Comprehensive documentation
- Error analysis
- Cycle time and process optimisation
- Visualisation
- On-site commissioning
Convince yourself of our know-how and many years of experience by optimising and adapting your programmable logic controllers. Irrespective of whether you want to integrate new functions and systems into existing systems or a completely new project is coming up – we develop the right software solution for your needs.